曲轴设计与加工过程介绍
引言:说起曲轴,我们能够想到的可能就是汽车发动机中的曲轴部件,其作用自然是承受连杆传来的力,并将其转变为转矩通过曲轴输出并驱动发动机上其他附件工作,是发动机中非常重要的组成部件之一。本文,我们主要来介绍一下曲轴设计与加工的过程。
曲轴是发动机中最典型、最重要的零件之一,其功用是将曲轴连杆传递来的气体压力转变为转矩,作为动力而输出做功,驱动其他工作机构,并带动内燃机辅助装备工作。这就意味着剧烈的加速和减速,并伴随高弯曲变形、高扭矩和振动冲击,导致非常高且多变的应力。如此极端化的应力需要精心的设计和计算、选择合适的材料以及批量加工工艺。
轴类零件在机械中的主要作用是传递动力和扭矩,同时也对轴上的其他零件起到支撑作用。发动机曲轴是发动机的动力元件,这就要求发动机曲轴有足够的尺寸精度和结构强度,因此对发动机曲轴进行加工时就要仔细考虑选择何种材料,使用何种毛坯成型工艺,加工过程分为哪几步,怎样进行热处理保证曲轴的机械性能等。一般的加工工艺流程是:确定零件材料和毛坯成型方式、确定加工顺序和加工基准、粗、精加工发动机曲轴的主轴颈和连杆颈、加工法兰孔和信号轮孔、热理、加工沉割槽、精磨主轴颈和连杆颈、抛光、检查尺寸结构并涂油入库。
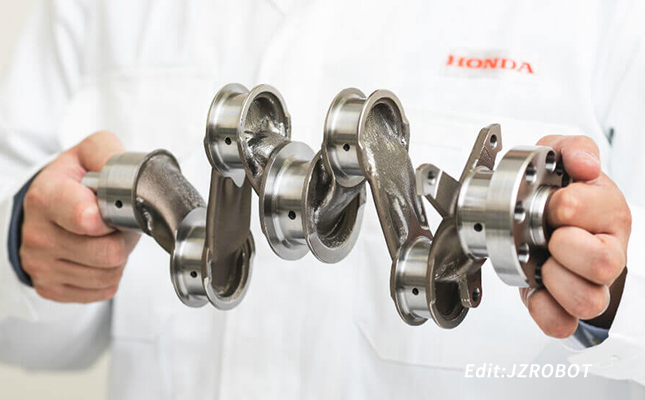
曲轴设计加工过程介绍
1、确定曲轴材料和成型工艺
(1)确定材料
目前阶段制作汽车发动机曲轴的材料主要是球墨铸铁和调质钢。球墨铸铁具有良好的切削性能,比较容易加工出合适的尺寸结构,其强度、韧性和塑性可达到中等水平,具有较高的机械综合性能和良好的耐磨性与减震性,铸造工艺性能优良,也可通过热处理来改变其结构性能。除具备良好的机械性能之外,球墨铸铁的成本也比较低廉,制作同样规格的零件,球墨铸铁的成本仅为调质钢的三分之一左右,因此大多数汽车制造企业都选用球墨铸铁作为制造发动机曲轴的材料。国内的汽车制造商对球墨铸铁的使用也非常广泛,八成以上的中小型功率发动机曲轴的材料均为球墨铸铁。
(2)成型工艺
发动机曲轴属于结构复杂的零件,一般都会预先将材料进行成型处理,加工成零件的大致尺寸再进行精细加工,成型方式有两种一种是模锻成形,一种是铸造成型。模锻成形加工出的毛坯尺寸精度较高,后期的加工余量小,且锻件内部的锻造流线按锻件轮廓分布,从而提高了零件的力学性能和使用寿命。铸造成型的毛坯需要加工的余量大,且对加工的刀具影响大,加工时还容易产生较多废气。因此选择锻造件作为发动机曲轴的毛坯。
2、确定加工顺序和加工基准
确定加工顺序时要遵循先粗后精、先主后次、先面后孔、基面先行的原则。加工基准分为粗基准与精基准,确定粗基准的原则是不以加工面为基准且粗基准不能重复使用。确定精基准时要遵循基准重合和基准统一原则,每更换一次加工基准就会使零件的尺寸精度降低,所以精基准应尽量保持统一。加工曲轴时,选择轴的两个端面为粗基准,在两端面上加工出中心孔,作为精基准。
3、粗加工、精加工主轴颈和连杆颈
发动机曲轴加工时的重点结构就是主轴颈连杆颈。此道工序加工工步多,加工耗时长,切削量大,且需要专用夹具和设备。一般的固定方式是用两个顶尖分别顶在两端面的中心孔,中心架作为定位支撑,以减小其加工时造成的精度误差。加工时控制切削速度和进给量,最好使用带有刀库的数控加工中心进行加工以减少换刀时长。
4、加工法兰孔和信号轮孔
加工法兰孔和信号轮孔时要注意保证孔和曲轴轴线的同轴度,加工时可采用增大顶尖和中心孔接触面积的方式减小轴跳动。加工深孔时要先钻一个定位孔,进刀方式要选择螺旋进刀,且确保加工时能够正常排出废屑,加工到一定深度时应将刀具整个退出,将孔内和刀具上的铁屑清理干净再继续加工。
5、热处理
曲轴在工作时,主轴颈、连杆颈部分需要传递较大的扭矩且要承受较大的载荷因此需要有较高的强度和韧性,所以热处理方式一般选择调质处理,即淬火+高温回火。这种热处理方式,能有效提高零件强度和收缩率,降低其脆性,并且能够消除加工产生的应力。热处理的顺序是先对连杆颈进行淬火处理,然后对主轴颈进行淬火处理。完成淬火之后再对零件进行加热,之后再冷却完成回火,经调制之后曲轴的洛氏硬度能达到45到60之间。
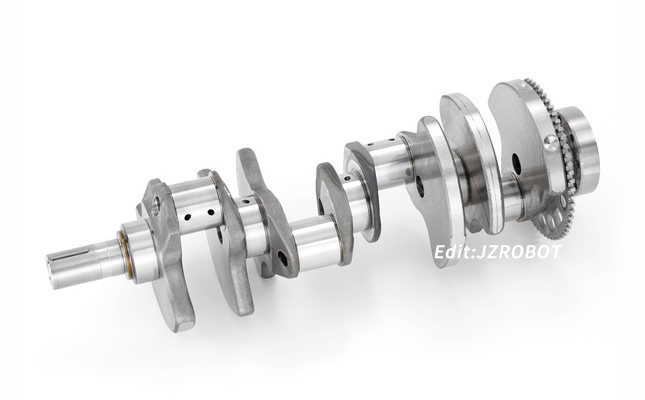
6、修磨中心孔
曲轴两端面的中心孔是精磨时的重要基准,应尽量保证两端中心孔轴线相互重合,中心孔锥角角度合理,因为顶尖属于精密夹具,所以中心孔的尺寸精度要求很高,否则会对顶尖造成破坏,在加工过程中也会因中心孔孔壁粗糙,发生轻微轴跳动,影响零件的同轴度。中心孔在完成主轴颈和连杆颈的加工和经过热处理后会有一定的磨损变形,影响之后加工工步的尺寸精度。所以在精磨之前,要对中心孔进行修磨,消除误差。一般的修磨方式有:通过硬质合金顶尖、铸铁顶尖以及用中心孔磨床修磨。发动机曲轴有较高的精度要求,因此采用中心孔修磨床完成修磨。
7、加工沉割槽
进行沉割槽的加工时可选用不同的滚压头来加工曲轴的各个沉割槽,由于各个滚压头的扭矩不同,可以实现对曲轴的沉割槽的同时加工,极大地提高加工效率。加工过程中使用感应接头来控制加工余量,通过监测滚压过程中刀具震动情况和刀具转速,来分析滚压过程中刀具的工作状态,确保加工精度。
8、磨削加工
虽然不同车型的发动机曲轴各部分的尺寸精度要求不同,但是曲轴属于精密零件,一般加工达不到其精度要求,所以为保证其尺寸精度,要对主轴颈和连杆颈进行研磨加工。以中心孔作为精磨加工的精基准,先加工主轴颈后加工连杆颈。加工时用中心架对其进行固定,并配备进给连杆和止推轴承,边加工边测量,确保精度要求。磨削加工时工件与刀具摩擦会产生非常大的热量,容易烧伤零件的加工表面,所以磨削时应采取良好的冷却措。
9、抛光处理
精磨之后曲轴加工大致完成,由于加工过程中由于刀具磨损和固定夹具会在工件表面产生螺旋线或者夹痕,因此需要抛光处理。抛光带磨削力高,具有较好的强度和柔韧性,能够达到精密的抛光效果,有效去除工件表面损伤。
10、曲轴强化工艺
曲轴的机械加工步骤完成之后,为保证曲轴的表面硬度、耐磨性和抗咬合性,应对其进行强化处理。经过软氮化处理之后的曲轴,氮碳共渗层薄、摩擦系数低,其内部形成经过塑性变形形成强化层,强化层内形成较高的残余应力,整体的抗疲劳强度得到提高。
曲轴零件的主要加工表面是主轴颈外圆面以及连杆上下、左右表面。因此,对于曲轴来说,加工过程中的主要问题是保证主轴颈外圆面的同轴度,处理好孔和平面。
以上这些内容就是关于曲轴设计与加工的相关介绍了,相信大家在看了上面的介绍之后,对曲轴设计已经有所了解了。如果还想了解更多曲轴设计的知识,以及自动化设计的知识,可以关注我们的公众号。